Cheryl Miller posted on November 22, 2022 07:41
Pivoting Wire Belt "Dump Conveyor" for Bakery Rejects
Sanitary, wash down and hygienic too.
Multi-Conveyor recently built a 9’ x 42” sanitary food-grade stainless steel wire belt conveyor with a pivoting discharge end. The pivot is used to dump batches of rejected bakery product from proceeding down the line. Replacing an existing transport conveyor, this section was engineered to retrofit seamlessly into the customer’s current production layout.
In the video, Tom Wright, Sales Account Manager, explains: “The customer has an existing conveyor they’ve asked us to break apart to put an intermittent conveyor that provides a form of a reject on one of their bakery lines. When they get a bad batch or group of bad product, they dump into a tote or bin. The pivoting end comes down allowing them to convey off into a tote or bin. When that group is done being rejected, the discharge end pivots back up again and transfers to an intermittent transfer (provided by the customer) to move on to the next part of the existing conveyor line.”
A pneumatic A.O.B. (air operated box) enclosure houses controls for the air-actuated reject to pivot in the up or down position. A manual override selector switch was also built-in so the operator can pivot the discharge on demand. This electrical enclosure will be mounted remotely for operators to easily select automatic or manual override as required.
The wash down system features ground and polished welds throughout, welded internal frame spacers, and special sanitary floor supports. In the video, Dennis Orseske, Estimator, Multi-Conveyor, further explains: “This is one of Multi-Conveyor’s Level 5 sanitary jobs. If you look close, every one of the bosses are welded and self-ground to a certain radius. There are no lock washers. All in place, spaced off (connecting plates) in between each section, so nothing will gather up inside. We have bearing caps that keep grease from gathering inside and we have what we call clean-out holes so when you go to clean your conveyor you can spray (water) inside. This is an open mesh top so you can spray all the way through it.”
Safety was also factored into the system. Dennis continues, “We have cleanout holes so you can’t get your hands or fingers in there for safety reasons. We have a return boot plus a support for the chain. When this section (he points out in the video) drops downward the conveyor will clean itself out (of product). As you can see here, we have our shafts coming through. There is a sanitary, removable finger guard on the shaft so you can’t get your hand caught up in there.”
To minimize particulate accumulation and promote easier cleaning, unique stainless steel hygienic articulating adjustable pad style feet complements the sanitary design. Dennis sums it up, “We have a sanitary adjustable foot which is very unique. Bossed and no threads are exposed whatsoever.”
Multi-Conveyor typically provides an end-drive profile at the end of the discharge, but because of the pivot conveyor having to raise and lower, we needed to get that mechanism away from the pivot, so we used a center drive.
A near foot incline in elevation required Multi-Conveyor to build a special extended-up, notched frame to support a customer-supplied smaller wire mesh product transfer that completes the smooth transition from the new pivoting discharge back onto the existing line.
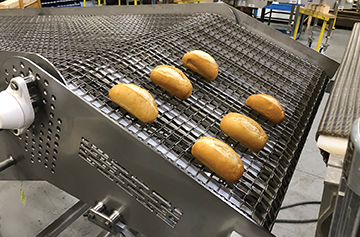
View this system in action at https://youtu.be/5XkSNFmlZJ0.